Summary
Advanced analytical techniques help manufacturers reduce inventory levels of parts required in manufacturing activities while maintaining confidence that they will not run out of parts. Mosaic was tapped to help a manufacturing company in the semiconductor industry develop an inventory management analytics system.

Take Our Content to Go
Introduction
Many organizations have an overload of data, software, reports, and all the associated processes & staff to manage its data assets. The inability of these organizations to develop a forward-looking-analytics plan not only costs the firm with storage & hosting, but the loss of market share, competitive advantage, and customers permeates the culture. A lack of machine learning knowledge and experience leads companies to not knowing where to deploy these techniques, and have them scrambling trying to figure out where to get started to get predictive/prescriptive value.
In the following success story, Mosaic helped a global, diversified semiconductor manufacturer catalog their supply chain data & software assets, map out the most impactful use cases on an achievable analytics roadmap, and developed a prototype tool powered by predictive analytics to aid in their inventory management decisions.
Inventory optimization is a complex component of supply chain management that is vulnerable to many internal and external factors. It involves having the proper inventory to meet demand and buffer against unexpected disruption while avoiding wasteful surplus. A successful inventory optimization process will accurately forecast demand and respond quickly to risks and opportunities to maximize financial returns. It is also efficient in the tools and data it relies on to produce accurate output.
As experts in machine learning and artificial intelligence, Mosaic was tapped to help a manufacturing company in the semiconductor industry solve the complex problem of optimizing their inventory for both future orders and historical demand rates. Mosaic helped the company create an actionable plan for managing its inventory, which was hindered by an overwhelming amount of data, too many tools, and inefficient processes.
The company sold millions of products to thousands of customers; therefore, maintaining demanding Service Level Agreements (SLA) and customer expectations was a constant challenge. Mosaic used prescriptive analytics (optimization) techniques to map the firm’s data to desired outcomes and infrastructure, helping them shave tens of millions on the bottom line while providing a streamlined customer experience.
Deploying Inventory Management Analytics
Manufacturers of expensive and complex industrial equipment often allow customers to configure hundreds of individual options on their products, leading to thousands of permutations. This means manufacturers need to manage inventory of hundreds or thousands of individual parts and components. A stockout of a single part can delay a customer’s order.
Advanced analytical techniques help manufacturers reduce inventory levels of parts required in manufacturing activities while maintaining confidence that they will not run out of parts. This is done through a combination of demand forecasting, which should use machine learning algorithms to predict what your future sales are based on past behavior and associated variables like seasonality, product attributes, customer attributes, and geography, and optimization algorithms that balance the costs of holding excess inventory against the risks of unfulfilled or delayed orders due to stockouts.
Machine learning and advanced analytics presents many benefits in improving supply chain decisions including:
- It allows organizations to ingest more data points
- It makes projections more accurate
- It automates the process of having to input numbers
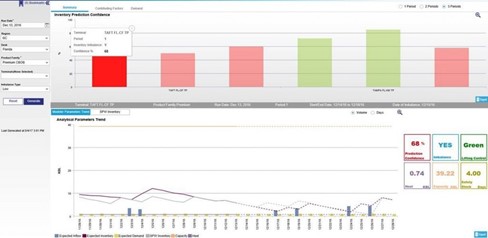
Scope of Work
To solve this problem, Mosaic recommended a myopic inventory policy with optional lot sizes. The previous policy only considered the direct service level implications of the current ordering decision based on known and predicted demand during the period covered by the order decision, known as the “coverage window.” It failed to account for the unknown demand, which the manufacturer knew disrupted their supply chain heavily.
Our experienced team of data scientists went to work to develop a pilot inventory optimization tool, powered by custom analytics, for the parts and components used in the manufacturing of their product. Mosaic aimed to automate the selection of inventory policy parameters for each part to minimize the risk of stockouts and reduce average on-hand inventory levels.
Developing a Successful Optimization Model
Mosaic’s scope of work involved a custom optimization model for recommending the minimum reorder quantity and the reorder point for each part or component used in manufacturing the two main products built by the customer. Each product can be configured in numerous ways, and each configuration has its own unique parts list – presenting ample opportunity for advanced optimization techniques.
The manufacturer’s needs included:
- customer-specific constraints on trace element amounts in delivered product,
- raw material lot schedules and trace element contents,
- objectives related to consistency of finished product for customers over multiple deliveries.
Ultimately, this model could then be used for an estimated 8,000 parts in the manufacturing process.
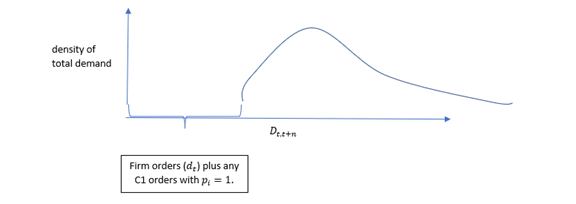
Demand Forecasting Refresh
Upon review of the customer’s demand forecasting processes, it was determined Mosaic would help automate & refresh these projections with fresh approaches.
Methodology
Mosaic’s customer operated in a B2B environment where orders had variable lead times from a few weeks to close to a year. This meant that at any given time, the customer had partial information about their upcoming demand for specific parts. Demand was roughly broken down into 3 categories:
- Known demand – upcoming part-level demand based on the manufacturing schedule for existing firm orders
- “Known unknown” demand – demand estimated based on orders still being negotiated and finalized; sales teams generate and update these estimates along with confidence levels on whether each potential order will close
- “Unknown unknown” demand – demand associated with “pop-up” orders that are not currently under negotiation but may arise and close within the delivery lead time for a given part or component
The “unknown unknown” was to be estimated based on historical volume. Over time, demand moves from unknown to known. The challenge presented to Mosaic’s data scientists was being able to look out over a part’s lead time. In the manufacturing industry, personalization often affects the length of time it takes to build the product, which extends lead time and makes it harder to plan for.
The Mosaic team was challenged with this question: How do we estimate the proportion of a part’s demand that is still fully unknown?
Key Assumptions about Demand
For the purposes of the model, the first assumption was that 100% of historical demand was still “unknown unknown.” The new forecasting model computed safety stock to cover “known unknown” plus all historical demand and did not adjust for known demand. This means the manufacturing company would have to pay the end customer if they don’t have enough product on hand to meet promised orders.
The result was an overestimation of necessary safety stock, which could be detrimental because more safety stock on hand means higher costs associated with keeping excess inventory in the warehouse than needed. On the other hand, this buffer also enables the company to provide a better customer experience and pay less in late shipping fees.
The second assumption was that 100% of historical demand was either “known unknown” or “unknown unknown.” Historical data would be adjusted if the known unknown was exceptionally high. The algorithm computed the safety stock max based on historical data to cover the “known unknown” low and did not adjust for known demand.
With this assumption, the model weighs the less time it takes to make a product vs. having that product on hand, providing a more accurate estimate of safety stock, and helping the manufacturing company lower lead times.
The third assumption was to proportionally adjust historical demand based on lead time. For shorter lead times, the model assumed that a larger percentage of demand was already known and/or “known unknown” and reduced “unknown unknown” accordingly. This meant less of a focus on historical sales information (demand), and more of a focus on more efficient production processes.
The fourth and final assumption proportionally adjusted historical demand based on lead time, using the same historical demand adjustment as the third assumption. The same logic as assumption 2 was applied with reduced historical demand, resulting in minimal safety stocks, especially for low lead time items. The reduction amount in this scenario is subjective.
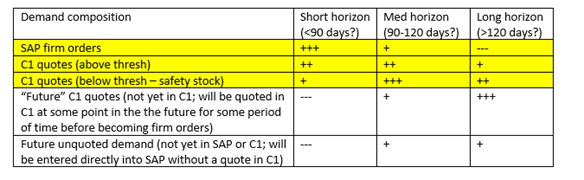
Inventory Policy Recommendations
Predictions helped determine the target safety stock, reorder point, and order quantity for each SKU based on past demand, known orders, and forecast orders. Independent inventory policies were recommended for each part at each manufacturing facility.
To predict future inventory levels and safety stocks, Mosaic inputted the following combination of data points:
- Historical volumes
- Booked orders
- Forecast orders (demand forecasts)
- Data about the SKU (e.g., lead times, target in-stock rates)
These variables and data points helped make the inventory policy more dynamic beyond known and predicted demand. The manufacturing company could control this to understand how to efficiently and effectively stage their inventory.
The proposed model generates independent inventory policy recommendations for each included SKU. Mosaic’s custom optimization model sets the reorder point and order quantity to achieve specified SKU-level in-stock rates. This was integral to ensuring order fulfillment, shifting sole reliance on forecasted demand, so the model was factoring more operational conditions providing more accurate visibility into the supply chain.
Inventory Management Analytics Conclusion
There are various ways to use machine learning to predict demand & stage supply for organizations in the manufacturing space and beyond. The problem presented by the manufacturing company required a need to be more precise in managing inventory, particularly in a B2B space. Mosaic’s solution was to deploy custom analytics techniques to better optimize the company’s inventory management decisions.
Mosaic has helped the manufacturing company meet demand volatility and supply chain challenges head-on by automating demand forecasting and inventory planning while recommending reordering activities. The prototype app developed demonstrated to business stakeholders the value that an optimization model can provide as an input to the production planning process. Mosaic’s tool was deployed into production, and the manufacturer uses it to set inventory policies.
By converting product configuration-level demand schedules and producing future projections to demand distribution, this inventory optimization tool has the potential to make the manufacturer more competitive in their space.