Summary
Mosaic built custom ML & AI models for a leading express shipping company to optimize their overnight shipping operations.
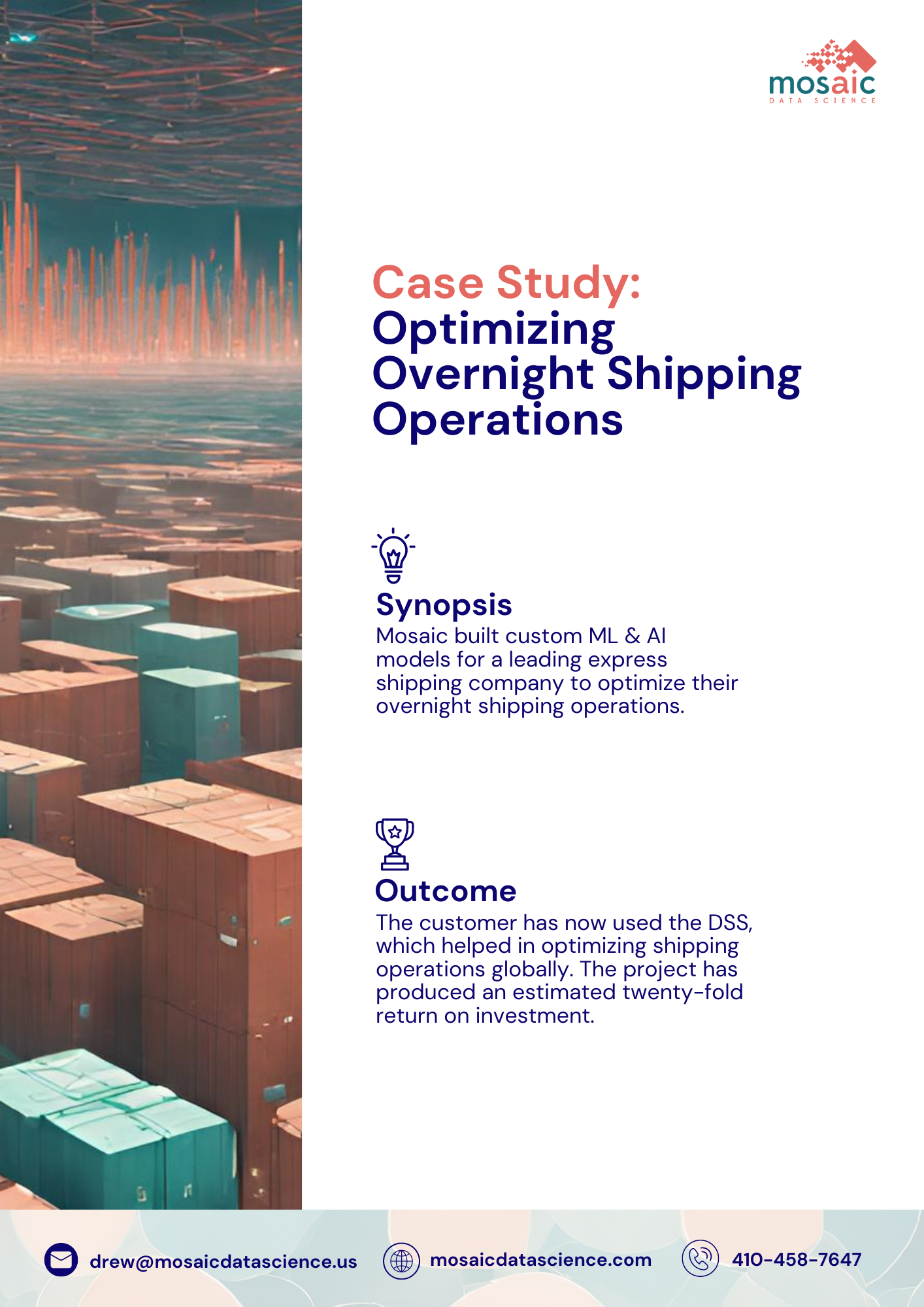
Take Our Content to Go
Background
The customer operates about 100 large jet aircraft. These aircraft do the same thing every night:
- Arrive at the customer’s main hub from points of origin around the country.
- Unload their cargo (which is then sorted).
- Receive new cargo.
- Depart for destinations around the country.
Cycle times are critical. Compressing the time between an aircraft’s arrival and departure would let the company offer better service and capture more revenue. Avoiding mistakes that cause delays is extremely valuable, as a late aircraft can result in tens or hundreds of thousands of dollars in late-delivery fees. Common mistakes causing delays included
- Ramp congestion
- Sending an aircraft to the wrong gate.
The customer had three goals:
- Reduce mistakes resulting in delays.
- Make sure the nightly sort goes smoothly.
- Reduce jet-fuel consumption.
The customer retained Mosaic to design and implement a decision support system (DSS) to help the customer achieve these goals.
Approach
Mosaic implemented a DSS at the customer’s hub. The DSS helped the customer in four ways:
- It gave decision makers situational awareness across all operational areas, including ramps, the ramp control center, and the air traffic control coordination group. This greatly reduced previously common mistakes.
- It provided a playback feature that lets decision makers review an operation shortly after its completion. This helped decision makers perform root-cause analyses that let them discover new ways to make traffic flow better, keep ramps uncongested, and avoid coordination failures with air traffic control. Playback also revealed opportunities to improve coordination with air traffic control about runway assignments. When this coordination happens, it can reduce the time between first and last departures by a very valuable 10 or 15 minutes.
- It used a variety of customer data feeds and a complex optimization algorithm to compute and recommend ideal engine-starting times for the customer’s aircraft. These recommendations helped the customer minimize the time an aircraft idled its engines before departure. Rather than taxiing out to a runway congested by other departures and idling its engines there, each aircraft now waits its turn with its engines off, for as long as possible.
- The DSS’ user interface (UI) was configurable by design, so each decision maker could tailor the UI to their workflow. This feature helped decision makers adopt and make the best possible use of the DSS.
Results
The customer has now used the DSS for eight years and helped in optimizing shipping operations globally. The project has produced an estimated twenty-fold return on investment in that period. Annual savings are estimated to be five million dollars. Jet-fuel savings alone are estimated to be several million dollars.
Contact us here if you are looking to optimize your shipping ops!